Aluminum foil manufacturing process
The aluminium foil manufacturing process can be divided into 9 steps, that is casting – uniform treatment – surface cutting – hot rolled – cold rolled – foil roiling – wash winding – annealing – cutting.
1, Casting
The production castings, fine aluminum ingots (to remove impurities) suitable for for rolled, heated to melt into molten metal. Some manufacturers will add the rolling debris to formulate different purity aluminum ingots, but the total purity is guaranteed. Molten metal generally use rolling to become billets by continuous casting.
2, Uniform treatment The cast billet is maintained at a high temperature close to the melting point (20-30 hours), is homogenized. As a result of this treatment, the deformation in the casting can be well eliminated, and the impurities also dissolve in solid solution and the impurity distribution becomes uniform.
3, Surface cutting Billet has irregular surface and the oxide layer.. So it is need to be cut about 8-10mm’s thick.
4, Hot-rolled After the billet is heated at about 5000C, the billet is put on a rolling mill and hot-rolled. Rolling about 10 times, pressure to about 3-5mm’s thick, rolled into coils (hot coil). During rolling, rolling and recrystallization occur at the same time, the foundry structure is destroyed, resulting in rolled structure. When hot-rolled, the crystal grain size of the high-purity aluminum is about 0.5 mm.
5, Cold-rolled The hot coil is cold rolled at about 800C while cooling. After about 3 times, rolled to about 0.5-0.6mm’s thick, roll into coils. This is what we commonly called the original foil.
6, Foil rolling The original foil is cold-rolled into thin foil by a high-precision rolling machine. Aluminum can be rolled to minimum of 5μ. When rolling about 10μ or less, two overlapping rolling can be used. The original foil achieve the required thickness by rolling several times.
7, Wash winding The rolling is finished, the rolled oil is washed away, and then wound into rolls.
8, Annealing Hard foil is generally through heat treated, annealed to semi-hard or to the end of recrystallization. Sometimes provide a very soft foil by high temperature annealing close to the melting point. Annealing is an important process that determines the nature of the foil. In addition, in order to impart special properties to the aluminum foil, annealing is also carried out during the rolling.
9, Cut the foil Aluminum foil produced only by rolling has irregular edges. Moreover, most users require foil that is narrower than the maximum width of the rolling. Therefore, not only about the edge of the foil, but also the rolling direction should be cut. This process is called cutting the foil, it is sometimes also carried out before annealing.
Reprinted from:https://www.aluminum-foil.net/aluminum-foil-manufacturing-process/
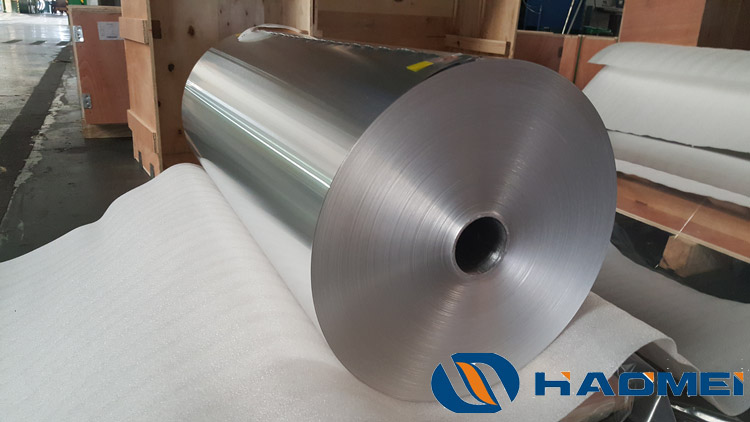
2, Uniform treatment The cast billet is maintained at a high temperature close to the melting point (20-30 hours), is homogenized. As a result of this treatment, the deformation in the casting can be well eliminated, and the impurities also dissolve in solid solution and the impurity distribution becomes uniform.
3, Surface cutting Billet has irregular surface and the oxide layer.. So it is need to be cut about 8-10mm’s thick.
4, Hot-rolled After the billet is heated at about 5000C, the billet is put on a rolling mill and hot-rolled. Rolling about 10 times, pressure to about 3-5mm’s thick, rolled into coils (hot coil). During rolling, rolling and recrystallization occur at the same time, the foundry structure is destroyed, resulting in rolled structure. When hot-rolled, the crystal grain size of the high-purity aluminum is about 0.5 mm.
5, Cold-rolled The hot coil is cold rolled at about 800C while cooling. After about 3 times, rolled to about 0.5-0.6mm’s thick, roll into coils. This is what we commonly called the original foil.
6, Foil rolling The original foil is cold-rolled into thin foil by a high-precision rolling machine. Aluminum can be rolled to minimum of 5μ. When rolling about 10μ or less, two overlapping rolling can be used. The original foil achieve the required thickness by rolling several times.
7, Wash winding The rolling is finished, the rolled oil is washed away, and then wound into rolls.
8, Annealing Hard foil is generally through heat treated, annealed to semi-hard or to the end of recrystallization. Sometimes provide a very soft foil by high temperature annealing close to the melting point. Annealing is an important process that determines the nature of the foil. In addition, in order to impart special properties to the aluminum foil, annealing is also carried out during the rolling.
9, Cut the foil Aluminum foil produced only by rolling has irregular edges. Moreover, most users require foil that is narrower than the maximum width of the rolling. Therefore, not only about the edge of the foil, but also the rolling direction should be cut. This process is called cutting the foil, it is sometimes also carried out before annealing.
Reprinted from:https://www.aluminum-foil.net/aluminum-foil-manufacturing-process/
评论
发表评论